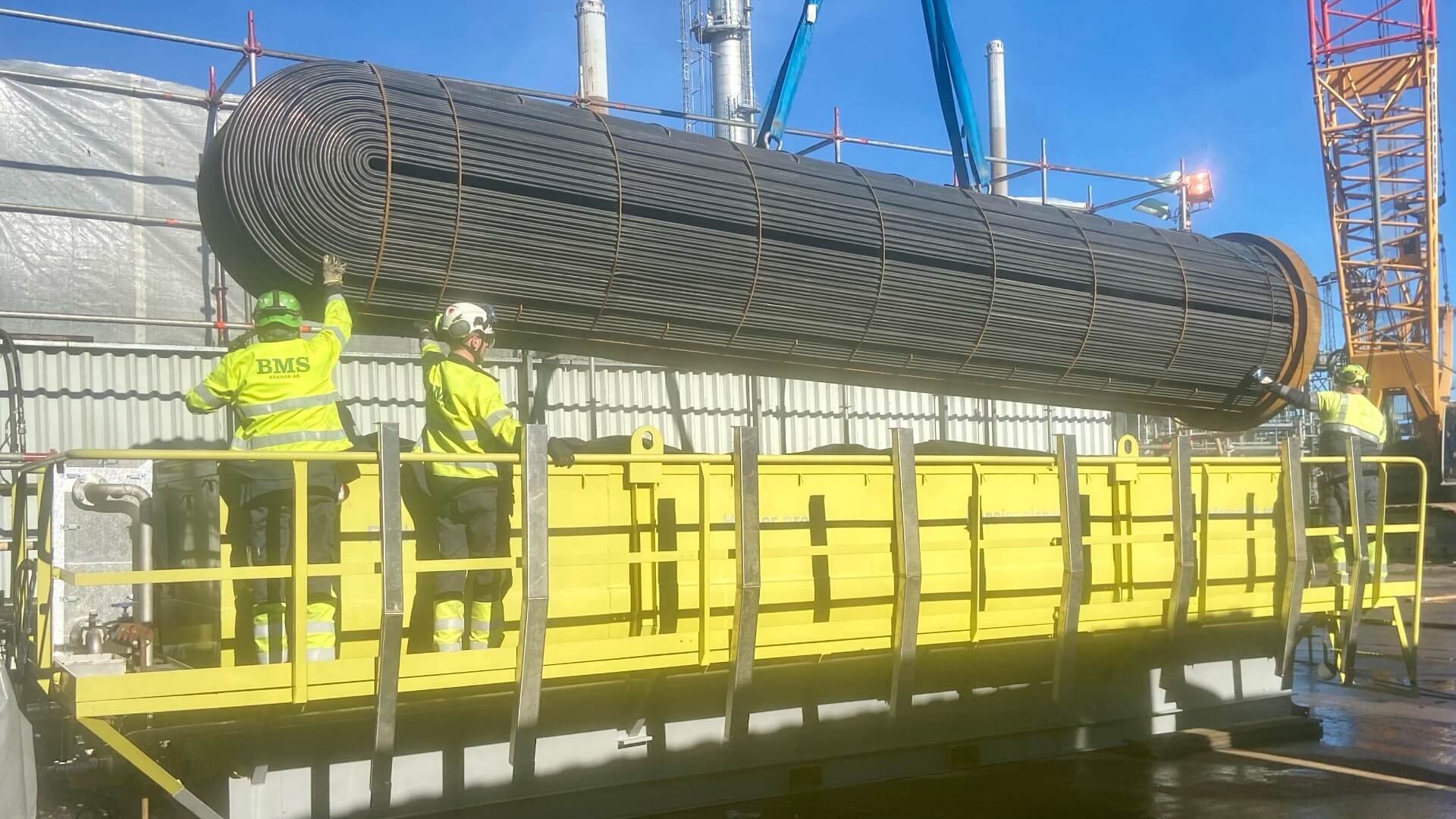
Preem is Sweden’s largest fuel company and refinery with its two facilities in Gothenburg and Lysekil. RecondConcept has worked together with Preem for several years to develop an efficient technology that enables the refinery’s heat exchanger to achieve a cleanliness level of close to 95% during cleaning.
The unique concept that RecondConcept offers is a tailor-made mobile cleaning bath that can easily be moved around the country via truck trailer. This bath can handle heat exchangers up to twelve meters long, has its own circulation pump and the possibility of heating with the help of steam.
Challenge and solution
With traditional high-pressure flushing of dirty heat exchangers, a lot of wear and tear often occurs. RecondConcept has managed to reduce this wear by deliberately halving the pressure through the tubes from the original 2,000 bar. However, it is the chemical process that is the biggest factor in a truly successful result. The chemical substance gets to the dirt deep inside the exchanger, surfaces that the high-pressure flushing has no chance of penetrating.
Depending on the type of dirt to be eliminated, different types of environmentally friendly chemicals are being used – all specially adapted for their specific purpose. When this process is carried out at the Preem refinery in Sweden, a chemical substance consisting of fruit acids as a base is being used. The reason for this choice is that the product is gentle on the environment and easy to handle.
In cases where there is a lot of dirt to be removed, we also use so-called ”bag filters” to catch the dirt during the cleaning process. By using this procedure, we partly reduce the consumption of chemicals but also maintain a high degree of efficiency during the process.
The Preem refinery in Lysekil – cleaning during maintenance stop
This specific assignment at Preem in Lysekil, Sweden, involves the cleaning of multiple tube heat exchangers, all of which have a surface of burnt, hard coked, oil. By submerging the respective heat exchanger in our custom-made cleaning bath, with the help of environmental friendly chemicals, a large part of the dirt can be softened and, to some extent, the coked oil can also be removed. When the tube exchanger is lifted out of the bath, it is high-pressure rinsed to remove the remaining coating.
Our working process at the Preem refinery
RecondConcept arrives in Lysekil with its custom-made cleaning bath on a trailer and establish ourselves at the refinery. Preparations are being made to be able to receive the first heat exchanger already on the same day.
The process is started by placing the exchanger in the bath. Then the appropriate chemical substance is added to the bath and the circulation is launched. A tarpaulin is placed over the bath to maintain the heat. The temperature is usually kept between 60-70 degrees Celsius and is produced using steam.
After the heat exchanger has been in the bath for approximately ten hours, a visual inspection of it is carried out. After the decision to take the exchanger out of the bath, it immediately undergoes the subsequent high-pressure rinse to remove the remaining coating.
Thanks to this efficient process, RecondConcept manages to clean up to two heat exchangers of this size per day/cleaning bath, and still achieve a very satisfactory cleaning result.
Millions of Euros to save with our method
Traditional cleaning of tube heat exchangers comes with large energy costs. Thanks to the cleaning system that RecondConcept has implemented at the Preem refinery in Sweden, the oil company can save approximately 20 GWh per year. With an estimated cost of 100 000 Euros per GWh, this corresponds to a saving for Preem of as much as two million Euros per year.